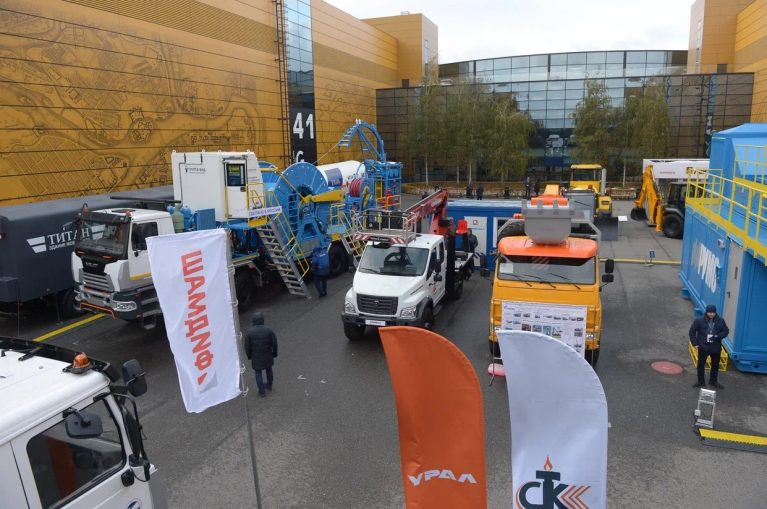
Research and development of special machines for the gas sector had seen a real breakthrough, which was demonstrated at the outdoor exhibition arranged during SPIGF 2023.
It really was like a show of futuristic machines. One of the most impressive exhibits was the 90 ton BELAZ 7558N dump truck. Its features are a combo of reliability, high capacity, and outstanding effectiveness, its fuel economy reaching 35%. Moreover, it is eco-friendly and LNG-based, has reduced maintenance costs (as such vehicles are delivered together with the infrastructure facilities) and extended gas engine operation life.
Sergey Nikiforovich, CEO of BELAZ, presented a comparison of the diesel and gas operation modes and resumed, ‘As diesel fuel prices keep rising, whereas LNG prices remain quite stable, we can expect a yearly economy up to 10 mln Russian Rubles per every BELAZ 7558N used.’
After the Forum ends, the dump truck from the exhibition will be included into the consignment of 10 gas vehicles of the same type that have already been ordered by one of the coal companies from the Kuznetsk Basin.
The Permian Synergy Factory presented another giant star − a portable electrically driven unit designed for main hole boring. The performance coefficient of its electric drive exceeds the parameters of the diesel one. Moreover, it is more eco-friendly and doesn’t require maintenance as frequent as its diesel predecessor, plus it is really space saving. Mikhail Simanovich, Chief Engineer of Synergy Factory, outlined the key feature of their prototype: ‘The unit includes only Russian-made elements − both the semitrailer and the mast have been produced locally. By the way, the hoist capable of 250 tons was specially designed by us, which we’re really proud of. I am absolutely positive that our project will spur the industry into switching to electric-driven drilling rigs.’
At its stand, Avantgarde Oil Services from Bashkortostan showcased a unique technology that isn’t used anywhere in the world yet − laser welding for well pipes. Today, everybody across the globe uses tapered pipe threads, which is not only expensive, but also not durable enough and sometimes not leakproof. In collaboration with IRE-Polus (Moscow), Avantgarde Oil Services invented a new tube welding technology based on a fiber-optic laser. This method requires the same time as the usual screwing. However, the final welding joint becomes more durable than the pipe body. ‘I hope this technology will soon become the most wanted one in the world,’ said Sergey Kopylov, Chief Structural Engineer of the project. ‘Tatneft already purchased two welding devices from us, and in 9 months of 2023 they’ve run down 120 drill pipes. In fact, with two devices you can run down 30 pipes a month and about 400 pipes a year.’
FID Group and FIDMASH brought to St. Petersburg their heavy-duty coil tubing plants. ‘We’ve made the first unit of this type, although a lower-duty one, in 1999 − and delivered it to Gazprom Podzemremont Urengoy. Since then, we’ve shipped 35 coil tubing plants to different Gazprom sites,’ explained Elena Novak, Deputy Director for Innovative Projects at MashOil. ‘The Russian unit is unique as it uses automated management systems in accordance with a preset algorithm. This leaves out human failures, damage that can be caused to the well and the environment, as well as unexpected situations at the well site. You won’t find such an automation level anywhere in the world.’
‘Russian engineers have been working continuously to further improve drilling options for these machines, and finally they can manage sidetracks, too. Now, up to 5.5 thousand meters of steel pipes can be run down at once, their diameter reaching up to 44 mm,’ mentioned Deputy Director for Business Development and Head of Sales Management at FIDMASH Sergey Yurenko. And he is sure that there is even more to come.
VolgoInvest and Kudesnik Group of companies brought to the Forum their leveling excavator UDS-224, based on the KAMAZ 43118 chassis and specially designed for the oil&gas sector. UDS 224 is expected to be released for serial production in April 2024 and is capable of covering long distances. It has got reduced turn radius and better maneuvering capacity. It supports engine switching to CNG and LNG, and the driver’s compartment is equipped with an air conditioner and a video+audio system.
Other manufacturers of special vehicles have focused on making the workers comfortable, too. Drivers’ cabins have been made more comfortable in another prototype designed for gas sites − the self-propelled mulcher TLP 4M 038, which is the only machine of this type stock-produced in Russia. In 2014, this machine was produced by the Barnaul-based Sibir-Technika, and now it is being used all over Russia. 300+ vehicles clear away unnecessary trees and shrubs in buffer zones around gas and oil pipelines and cut forest fire breaks. They are capable of mulching tree trunks with diameter up to 30 cm.
Toir, the Tyumen-based engineering plant, decided that managers need more comfortable workplaces, too. They designed a conceptual trailer-house for senior managers to work conveniently at the fields that are far away from common amenities. Thanks to the high quality of this portable facility, this chassis-based 10-meters house can be compared with a top-class hotel. It comprises a designer office zone, a kitchen, a bedroom, and a toilet. Evgenia Suprotivina, CCO of Toir Plant, explained: ‘About 95% of everything you see in this house has been made by us at our plant. This stand-alone house is supplied with water tanks and a septic tank. It can be connected to a generator but if necessary even a wood stove can be installed.’
Another noteworthy thing designed in response to the sanctions was displayed by RUMO. It was Russian first-ever gas-piston power plant RUMO 702 − a container module capable of 1 MW, working on natural gas. This electrical power supply facility was designed with the gas-piston combustion engine RUMO 502, which is the company’s own patented invention, produced at Nizhny Novgorod based factory. Another attention grabber presented at SPIGF 2023 by RUMO was the power section of 6PK32 piston compressor capable of 4 MW. This compressor unit was designed by the Senior Structural Engineer’s Service of the Factory and then patented, too.
The outdoor exhibition at SPIGF 2023 became a place to demonstrate samples of the most advanced equipment. Every stand and booth was all about import substitution. Upgraded loader excavators AMIR 3X, wheeled bulldozers and road machines by Lonmadi, state-of-the-art engineering inventions by Tekhno-Tsentr, products by Alapayevsk-based Stroydormash (drilling machines factory) and Altai-based Altailesmash (track and wheeled machines manufacturer) have become a perfect example of technical progress going through rapid and highly effective changes in the setting of aggressive restrictions.